Mess-, Steuerungs- und Regelungstechnik: Gefährdungsbeurteilung
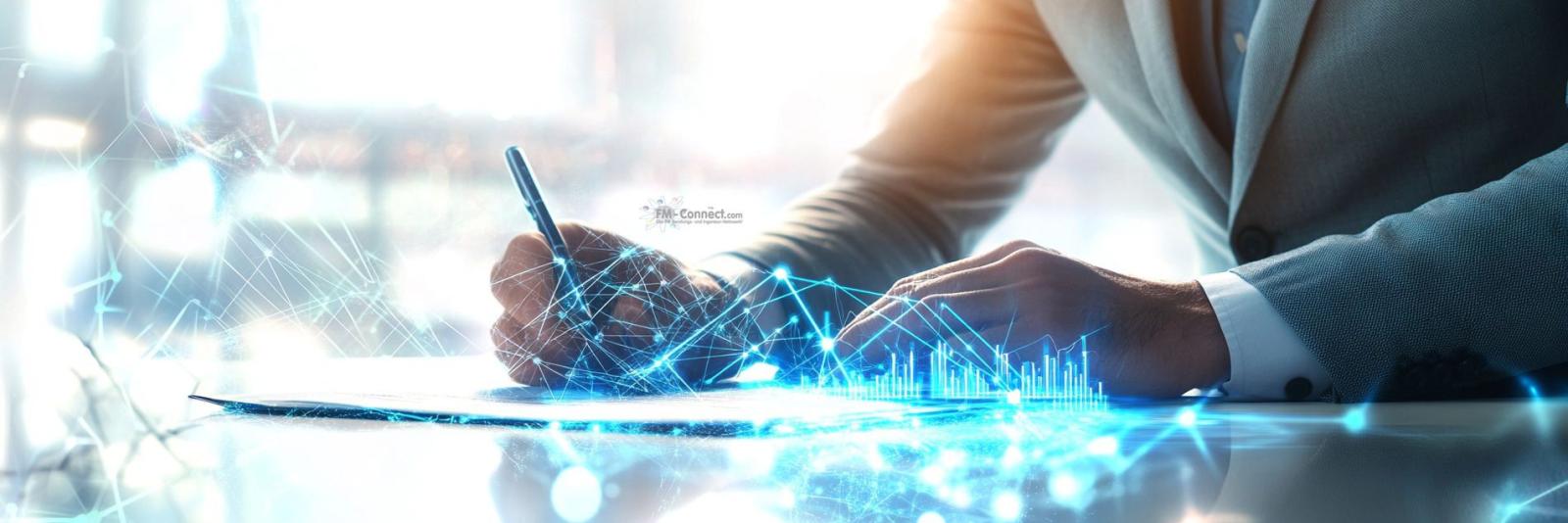
Gefährdungsbeurteilung zum Thema „Mess-, Steuerungs- und Regelungstechnik
Mess-, Steuerungs- und Regelungstechnik (MSR-Technik) ist in vielen Branchen unverzichtbar. Sie sorgt für die Erfassung relevanter Prozessdaten, die automatische Steuerung von Abläufen und die Regelung diverser physikalischer Größen (z. B. Temperatur, Druck, Durchfluss). Ob in der Prozessindustrie, im Maschinen- und Anlagenbau oder in Gebäudetechniksystemen – MSR-Technik sichert Effizienz, Produktqualität und Betriebskontinuität. Eine Gefährdungsbeurteilung für Mess-, Steuerungs- und Regelungstechnik ist erforderlich, da fehlerhafte MSR-Systeme zu gefährlichen Anlagenzuständen führen können oder bei Wartungsarbeiten erhebliche Risiken bestehen (elektrischer Schlag, Druck, chemische Stoffe).
„Mess-, Steuerungs- und Regelungstechnik (MSR)“ ist zentral für viele industrielle Prozesse. Fehlfunktionen oder unsachgemäße Wartung können zu gravierenden Sicherheits- und Gesundheitsrisiken führen (Überdruck, Übertemperatur, falsche Bewegungen von Maschinen). Eine Gefährdungsbeurteilung nach ArbSchG, BetrSichV und entsprechenden Normen (DIN EN 61508, 60204 etc.) ermittelt potenzielle Gefahren (elektrische, mechanische, softwarebedingte, chemische) und definiert technische, organisatorische und personelle Schutzmaßnahmen (Redundanz, Lockout-Tagout, Schulungen, regelmäßige Prüfungen). Dadurch werden Anlagen- und Arbeitssicherheit erhöht und Ausfallzeiten sowie Unfälle minimiert.